Outil de mesure pour la fabrication de composites
- Société Phalanx
- 3 sept. 2018
- 4 min de lecture
Airbus avait besoin d'encapsuler des capteurs faisant appel à des librairies externes et des capteurs câblés à des modules de mesure National Instruments dans un même moyen d’essai pour évaluer différents phénomènes physiques pendant la phase de fabrication d’un composite dans le but de le caractériser et détecter des gains de temps de fabrication.

Phalanx a utilisé l’environnement de développement LabVIEW, le matériel d’acquisition PXI avec contrôleur embarqué PXIe 8821 et le suivi de spécification via NI Requirements Gateway pour développer une application sur PXI robuste et intuitive.
Le pôle Recherche & Technologie d’Airbus Group Innovation (AGI) situé au sein du technocampus de Bouguenais joue un rôle essentiel au sein d’Airbus SAS. Afin de rester compétitif face à la concurrence, Airbus doit proposer des produits de meilleure qualité plus rapidement. Cela n’est possible qu’en misant sur l’innovation. AGI a sélectionné Phalanx afin que nous apportions notre expertise dans le domaine de l’acquisition et du test pour réaliser un logiciel d’acquisition de phénomènes physiques intervenant pendant le processus de fabrication de composites.

Un datalogger au service de l'innovation aéronautiqueDans un article publié le 9 mars 2016 dans L’Usine Nouvelle appelé « Et si l’aéronautique boudait les composites ? », nous apprenons que des verrous concernant les composites, et spécifiquement les opérations de contrôle, sont durs à faire sauter. En effet, il est écrit « Las, avec des prix qui restent élevés […], des opérations de maintenance délicates, un manque de flexibilité dans la production et un regain de vitalité du côté de l’aluminium et des alliages, les avionneurs les yeux rivés sur la rentabilité de leurs programmes pourraient se rabibocher avec le bon vieux monde de la métallurgie. ». Cependant, ces verrous peuvent être brisés si une innovation est mise en place dessus. C’est dans ce but qu’Airbus a souhaité mettre en place un datalogger afin de comprendre les phases « clé » d’un procédé de fabrication pouvant mener à une solution « 0 défaut ». Cette approche permet d’optimiser les fenêtres « procédé » et de réduire, de facto, les cycles et coût de contrôle.
La mise en place d’une solution National Instruments pour la partie matérielle d’acquisition et l’utilisation de l’environnement de développement LabVIEW, nous a permis de sortir une application à la hauteur de l’innovation demandée par Airbus.
Un choix de capteurs flexibles pour plus de modularité
Le matériel d’acquisition sélectionné (châssis PXIe-1078 avec contrôleur PXIe-8821RT) a permis de mettre en place un large choix de capteurs (du capteur LVDT en passant par des capteurs à courant de Foucault). Pour des raisons de compatibilité avec du matériel tiers, le système opératif Windows 7-32 bits a été installé. L’avantage d’un tel système opératif se situe dans la mise en place d’un moyen d’acquisition entièrement empaqueté dans ce dernier sans avoir la nécessité d’un PC déporté relié au PXI par Ethernet. Ce choix a aussi impacté le temps de développement, aucune programmation FPGA et Temps-réel n'a été réalisée. L’ensemble des acquisitions ont été implémentées grâce à l’utilisation des drivers DAQmx.
Le choix des modules PXI (cf. Figure 2) satisfait l’ensemble des acquisitions nécessaires mais également l’ajout de capteurs dans le futur. Aujourd’hui, un module PXIe 6363 se charge des acquisitions analogiques +/-10V, un module PXIe 4340 acquiert les données provenant des LVDTs, un module PXIe 4353 se charge de l’acquisition de thermocouples.
Le PXI possède également des ports USB autorisant ainsi l’ajout de capteurs tiers comme un profilomètre laser, une caméra Infrarouge et un matériel spécifique d’acquisition à Airbus sur ces derniers.
Le châssis peut aujourd’hui accueillir de nouveaux modules grâce à des emplacements disponibles dessus. Tous ces choix (système opératif installé, modules présents, slot de libre…) permettent à Airbus d’avoir du matériel d’acquisition modulaire pouvant évoluer dans les années à venir.
Ce choix de matériel permet d’avoir un panel assez large de capteurs permettant plus de flexibilité pour les essais à réaliser. Mais ceci n’est pas le seul facteur de flexibilité, le logiciel satisfait également ce point via le paramétrage des voies possibles. Phalanx a fait en sorte que ce paramétrage soit le plus intuitif possible et qu'il permette facilement l’ajout ou la modification de capteurs. Pour arriver à cet objectif, nous avons créé une interface où l’utilisateur peut venir sélectionner les capteurs qu’il souhaite utiliser dans une arborescence (cf. Figure 3). L’ajout de capteurs se fait grâce à une popup.
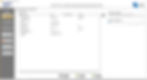
L’association du matériel National Instruments et de l’environnement de développement LabVIEW a favorisé la réalisation d’un banc d’acquisition flexible et modulaire.
Un historique d’événements et d’erreurs pour une maintenance aisée
Au sein de Phalanx, nous nous engageons à fournir un logiciel de qualité. Cet engagement est sans cesse en progression et peut se voir à plusieurs niveaux. Pour ce projet, il s’est particulièrement révélé au niveau de la mise en place d’un historique d’événements (événements utilisateur ou erreur). En effet, le milieu de l’aéronautique exige une qualité stricte. Cet historique est mis à jour à chaque fois qu’un événement singulier survient. L’utilisateur peut ainsi visualiser dans la page « santé système » les éventuels problèmes rencontrés mais également les actions réalisées depuis le lancement de l’application. Chacun de ces événements sont enregistrés dans un fichier texte.
Nous avons également mis en place plusieurs niveaux d’événements, "critiques", "non critiques", "à enregistrer uniquement" et "à ignorer". Si un événement "critique" survient, le logiciel se ferme en s’assurant d’arrêter correctement toutes les boucles parallèles fonctionnant dans le code et enregistre ce dernier.
Si un événement "non-critique" apparaît, celui-ci est enregistré, le logiciel n’est pas fermé cependant certaines boucles s’arrêtent (par exemple : arrêt de l’enregistrement) et celui-ci s’affiche dans la page "santé système".
Si un événement "à enregistrer uniquement" survient alors ce dernier est tout simplement enregistré, aucune autre action n’est réalisée.
Dans certains cas, des événements peuvent survenir mais ceux-ci n’entrainent pas de problème pour la fonctionnalité du programme, c’est pourquoi nous avons mis en place un système où certains événements peuvent être ignorés.
Conclusion et perspectives
Puissant de par sa modularité et ses performances, cet outil permet à Airbus d’analyser les phases vitales de la fabrication des composites dans la configuration qu’il souhaite.
Le technologie PXI associée à un développement sur LabVIEW ont permis de mener à bien ce projet.
Grâce à nos conseils sur le traitement des données, le pôle Recherche & Technologie d’Airbus situé à Bouguenais a décidé d’utiliser NI DIAdem afin d’analyser les données enregistrées au format TDMS pour, par la suite, en sortir automatiquement un rapport pour chaque essai réalisé.